齐翊 陈伟民 刘显著
(重庆大学光电工程学院 光电技能与系统教诲部重点实验室)
择要:
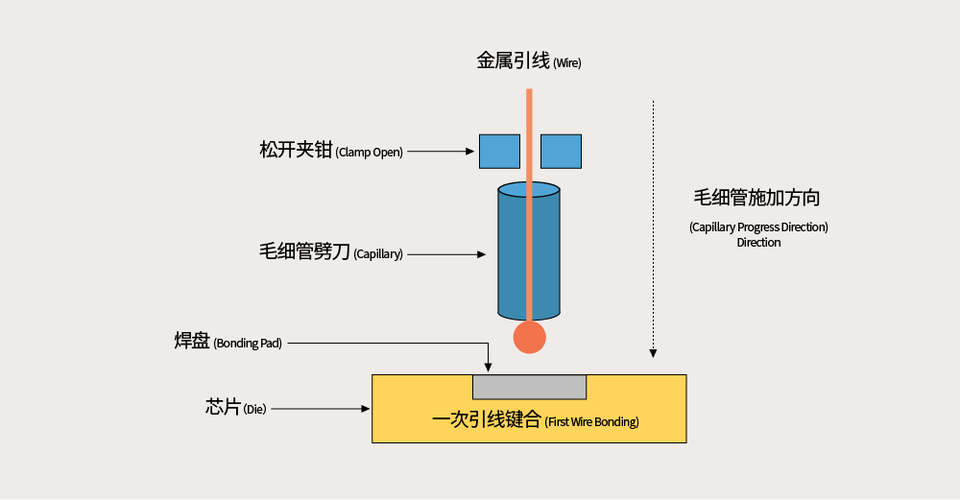
引线键合是半导体封装中实现芯片与封装引脚之间连接的关键技能,近年来半导体家当对更高的集成度、更高的可靠性和更低的本钱等方面的急迫需求,对引线键合技能提出了更高的哀求,因此引线键合的质量检测成为了担保半导体封装质量的关键技能。详细阐述了引线键合中质量检测的技能方法,比拟了各种技能的目的和技能特点,总结了各种方法的利用场合,并提出了键合线质量检测尚需办理的问题和发展方向。
统计表明,截止2014年仍有超过90%以上的芯片内连接由引线键合技能(Wire bonding)完成。引线键合中焊盘不洁、表面氧化、堕落和工艺参数不合理等都会产生毛病,进而产生裂纹、断线和焊点脱落等问题,这些问题会直接造成芯片的整体失落效或严重影响其可靠性。因此,在当代半导体集成电路器件的研制和加工中,都必须对引线键合的质量进行检测,以担保芯片内部连接的可靠性。范例集成电路芯片构造剖面图如图1所示。
1 引线键合的质量问题及紧张表征方法
要对引线键合的质量进行检测,就必须理解该技能的基本事理和工艺流程,节制引线键合中存在的质量问题,熟习这些质量的表征方法。
引线键合技能的基本事理是利用直径常日为几十至几百微米的高电导率金属导线(金、铝和铜等),在热超声浸染下按压在焊盘上,使焊盘与焊线的金属原子发生扩散,形成金属间化合物(Intermetallic Compounds,IMC),从而实现晶粒与引脚的连接。范例的引线键合工艺流程包括形球、超声加热、按压形成第一焊点、走线、按压形成第二焊点和分离等。如图2所示。
就引线键合的环节而言,焊盘的清洁、引线真个微球形成、引线的焊接、引线的走线,都可能产生质量问题。在焊接前如果焊盘被污染,就会在焊点内部形成几百纳米至几十微米的空洞毛病或微裂纹,从而造成键合失落效。在引线微球形成时的放电电流不得当,就会造成图2(a)中的微球尺寸超标或形状不规则,导致后续的焊球变形和焊盘产生裂痕。如果在图2的第一焊点(c)和第二焊点(e)引线压焊过程中,施加的压力、超声的强度与频率不恰当,会导致焊盘变形乃至产生裂痕和虚焊。引线压焊过程中,焊盘与焊球的位置识别偏差会导致焊点错位和脱焊等问题 [9] 。在图2的走线(d)过程,引线长度和空间布局不合理,就会发生引线塌陷和搭线短路等严重问题。
就键合后的注塑环节而言,其填料和固化工艺等,也可能引起键合的质量问题。如填料内存在气泡和不屈均等毛病,就会在注塑后产生较大的内应力,从而可能在器件后续利用中造成引线的断线或焊点的脱落,对引线的键合质量产生间接影响,影响其利用的可靠性。
在以上引线键合质量问题中,内应力断线和焊点脱落等问题反应了引线键合的力学特性,可以用动态或静态机器参数加以描述;断路和电参数变革问题反响了引线键合的电学特色,可以由电感和电容等电学参数加以描述;空洞毛病和微裂纹等问题反响引线键合的微不雅观描述,可以由显微成像得到的微不雅观描述特色来描述;引线塌陷和焊点错位等问题反响引线键合的整体描述,可以由整体描述特色进行描述。因此,引线键合的质量检测,可以归结为机器参数检测、电学参数检测和描述特色检测三大类。
2 机器参数检测方法
合格的键合线必须在实现有效电气连接的同时具有较好的机器性能。良好的机器性能不仅是正常事情的基本担保,同时也是芯片封装长期事情可靠性的根本。因此对引线进行机器性能的检测是评价键合线质量的根本。应力和振动是两种紧张的机器检测手段。
2.1 静态机器参数检测
静态机器参数的检测可以用于快速评估键合线的整体键合强度,创造脱焊和虚焊等问题。针对键合线的应力检测,引线拉力测试(pull test)和球剪切力测试(shear test)是最基本手段。在这两种方法的根本上,为理解决工业生产检测对速率和非毁坏性的哀求,还发展出高压空气吹检法和焊球成型过程压力测试法等。
引线拉力测试是丈量键合线强度最大略有效的方法之一,并被中国的国家标准和美国国家标准(MIL-STD-883)等广泛采取。该方法是用一个小勾勾住引线,测试时拉力的施加浸染点浸染于内、外两个焊点的中间部位,拉力的施加方向垂直于两焊点连线的垂直方向。在非毁坏性试验时不断增大拉力,当拉力到达标准规定值而引线未断裂或焊点未脱落,解释键合强度符合哀求,末了轻轻移开小勾。在毁坏性试验中,不断增加拉力直至引线断开或键合点脱落位置,此时得到的数值,即为极限键合强度。方法事理图如图3所示。
球剪切力测试(Ball shear test)是用一个平面的剪切刀,平行于焊盘向焊球施加推力,使焊球被剥离的力便是键合剪切力。球剪切力测试事理图如图4所示。
引线拉力测试和球剪切力测试除了能够通过拉力和剪切力评价键合质量之外,经由测试后脱落的焊盘还可以用于研究键合界面处金属间化合物的成长情形,进而优化键合过程的工艺参数或剖析改进键合股料。这些进一步的剖析常日须要借助材料剖析手段或下面的显微成像检测方法,如图5所示。
高压空气吹检法是一种引线拉力测试的替代方法,该方法利用高压空气自下而上吹过键合线,通过空气流动为引线供应拉力。该方法可以同时对多条键合线进行检测,但该方法不能供应精确的引线键合强度数据,只能作为定性的检测手段。
引线键合过程中须要将焊线材料压在焊盘上,并供应能量实现两种材料的键合。键合过程中焊接头压下时压力的大小和冲击变革过程直接影响焊球的质量。对该应变的大小和位置等参数进行检测也是一种评价焊接质量的有效方法。检测焊接时冲击过程的冲击力曲线和多次焊接时压力的差异可以用于提高键合线的整体质量。这种检测方法紧张通过在焊接机操作臂上增加压力传感器或在焊盘周围支配压力传感器的办法实现。在利用这些方法丈量得到的压力参数时,可以通过统计剖析的方法探求最优工艺参数,或利用多个传感器得到的数据剖析焊球的位置和成型质量等。
2.2 动态机器参数检测
动态机器参数检测可用于评价键合线整体性能及其疲倦特性。振动检测可以分为外加勉励振动检测和超声焊接过程振动检测。个中外加勉励振动检测是对完成焊接的键合线施加振动勉励源,检测键合线振动旗子暗记。超声焊接过程振动检测是检测超声焊接时焊接臂或焊点振动。
电磁共振测试法(electromagnetic resonance test)利用载有互换电旗子暗记的导线在磁场中受交变的安培力,引起键合线共振从而实现拉力测试。不同长度、粗细的键合线具有不同的共振频率,为了在测试中为引线供应足够的拉力,Michael Pecht等人提出利用一个具有一定频率带宽的互换勉励旗子暗记,引起被测键合线发生共振。实验事理图如图6所示。
微机器冲击法(Force Detected WireVibration Analysis)是由一个探针供应震撼勉励旗子暗记,另一个传感探针采集键合线的震撼旗子暗记,从而检测焊点和键合线的质量。个中供应勉励旗子暗记的探针打仗键合线的末端,用于检测的微探针打仗键合线中间。通过这种方法,H. Luo等人建立了键合点键合状态与键合线震撼旗子暗记频域特性的关系,研究表明键合存在机器连接毛病时,旗子暗记频域特色峰的幅度成比例低落,且特色峰向高频移动。
超声键合和热超声键合是引线键合中的基本方法,它们都因此超声波作为键合过程的能量源,超声波通过焊线机的操作臂通报到焊点处。对焊接过程的超声波旗子暗记进行采集和剖析是评价焊接质量的主要方法之一。在焊接机中,超声波的产生常日便是通过驱动压电材料实现的,将该压电材料同时用作传感器或者增加专用的压电振动传感器是丈量超声旗子暗记的有效方法,也可以通过激光干涉的方法直接丈量焊接头振动情形。
键合性能良好的引线该当具有合格的机器性能,因此对引线焊接过程和焊接结果的机器性能检测是评价键合质量的基本手段。在引线键合技能发展中,引线拉力测试和球剪切力测试虽然方法大略,但运用最为广泛,具有很好的适用性和统一的评价指标。振动检测中,超声振动检测是焊接过程中实现焊接掌握必不可少的环节。电磁振动法、微机器冲击法等虽然具有一定的检测上风,但由于方法繁芜等缘故原由并未受到广泛运用。
3 电学参数检测方法
电学检测方法是建立引线或焊点质量与电旗子暗记之间关系的检测方法。
当焊点内部存在裂纹和空洞等问题时,焊点电阻、电感和电容等电学参数发生相应改变。因此,可以通过丈量焊点直流电阻或互换阻抗来进行焊点的毛病检测。键合线高频电参数剖析是运用于射频芯片等传输和处理高频旗子暗记芯片必要的检测方法。该类检测须要引线键合在经由分外设计的测试板上,通过高频勉励旗子暗记丈量键合线的单位长度损耗和阻抗等参数。也可以通过高频旗子暗记有限元仿真的办法对键合线进行仿照剖析。在半导体发光二极管中,还可以利用其p-n结的光生伏殊效应,采取交变光源照射待测LED芯片,在封装的短路支架上勉励出光生短路电流;通过非打仗检测支架回路中光生短路电流 I L1 的状态对芯片质量及芯片与支架之间焊接处的直流电阻值的变革做出判断,实现对焊点质量的非打仗检测。
当涌现焊点脱落、虚焊和断线等问题时,可以直接进行脱线故障检测。附加独立检测电路的脱线检测(lift-off detection)常用于主要功率型器件,为了担保器件故障发时诊断并及时对系统做保护而开拓的焊点故障实时检测方法。
4 描述特色检测方法
机器参数或电参数都是用间接或整体性的特色参数对引线键合质量进行评价,有方便、易操作和易标准化的优点,但每每不敷以对引起质量差异的成分进行确定和深入研究。因此直接对键合的局部或整体的描述进行成像检测就显得至关主要。
局部显微成像是利用高倍率光学显微镜和扫面电子显微镜等通用的显微设备,拍摄引线键合的局部特色,进而剖析键合质量。整体成像检测是键合质量检测方法中受到较多研究者关注的方法。随着图像采集和处理技能手段的快速发展,结合机器视觉的键合线图像检测法在工业中也得到了有效运用。除了以可见光图像或红外图像为根本的检测方法外,近年来还涌现了电磁成像法、激光干涉成像法和涡流脉冲热成像法等新的成像检测手段。
4.1 局部描述特色检测方法
局部描述特色直接反应键合层厚度、键合层材料结合和键合点局部描述等主要信息。局部描述特色的检测是通过显微成像方法实现的,包含高倍率光学显微镜(Optical Microscope, OM)、扫描电子显微镜(scanning Electron Microscope, SEM)、透射电子显微镜(Transmission Electron Microscope,TEM)、电子背景散射成像(Back-Scatter Electron image,BSE)和电子探针显微剖析(Electro-Probe Microanalyzer, EPMA)等,图7分别为五种成像手段得到的范例结果。
显微成像常日用于剖析焊点的表面描述、成型特点、研究新工艺或新材料下焊点的形成质量。个中SEM利用最为广泛。在进行键合股料剖析时,还可以结合X射线散射能谱仪(line-scan Energy Dispersive X-ray, EDX)、次级离子质谱剖析仪(Time-of-Flight Secondary Ion Mass Spectroscopy,Tof-SIMS),弹坑测试(Crater test) [41] 等材料剖析手段进行进一步研究。
4.2 整体描述特色检测方法
整体描述特色可用于评价引线键合的塌陷和几何参数不合格等问题。键合线的整体描述特色检测方法有光学成像法、X射线透射成像法和红外热成像法等。
X射线成像是利用不同材料对X射线的穿透能力不同实现成像的方法,它可以穿透封装外壳,对完成封装的完全芯片进行成像,并剖析内部引线的键合情形,因此可以用于事情中破坏的芯片检测。
红外热成像法常日用于大功率芯片的整体检测,该方法可以通过热量集中点位置的剖析,实现毛病检测。
基于光学图像传感器的键合线整体描述检测,由于具有可以实现在线自动化快速检测的特点,且图像传感器和图像处理技能发展迅速,因此受到了国内外研究者的重视。对封装中键合线的断线、丢线、偏移、焊线长度过短或过长、下垂和触碰等进行整体成像检测。随着集成电路的繁芜度和集成度的提高和对检测速率哀求的提高,近年来基于成像方法的键合线检测研究紧张集中在提高检测效率和精度、适应高密度或空间布局繁芜的键合线检测、优化图像质量、提高特色提取准确度和采取新的勉励源实现分外成像。
在图像处理和特色提取的算法优化方面,1993年Wang Q.W.等人提出利用神经网络算法预测键合线质量。1994年Khotanzad A.等人通过优化边缘提取算法,通过二维图像的剖析实现了焊球描述、焊球位置和焊线直线度等参数的剖析。1996年,Rajeswari等人通过优化图像增强算法和改进系统照明,设计完成了基于机器视觉的快速自动焊线检测系统。Kong F.Z.于2009年提出了利用小波算法实现低清晰度的芯片键合线图像去噪和增强,该算法办理了边缘图形清晰度低落时依然担保高精度的键合线识别。2013年Kong F.Z.等人将SIFT-MIC算法减少运算量,提高了提取键合线特色的效率。实验表明该方法具有对拍摄图像角度和位置不敏感的优点,同时具有很好的位置精度和丈量效率。
在提升检测效率方面,1992年Tsukahara H.等人为了提高键合检测精度,在一套图像采集系统中用两种光源对焊球和键合线分别进行图像采集和处理,从而实现了±5 μm、0.2 s的键合线检测。1999年Rajeswari等人通过系统剖析认为图像采集部分是限定引线键合监测系统速率的瓶颈。为了实现高速实时的检测,提出了分步采集的办法,并设计了干系的算法流程,终极通过边采集边运算实现了单次检测总韶光0.22 s的实时检测剖析系统。2007年Perng D.B.等人利用荧光光源实现了焊线检测中增强焊线在图像中的比拟度,增加了图像识别的准确性。并利用增强的焊线图像结合数学建模,实现了单俯视图识别焊线下垂。
在改进检测系统设计方面,1997年Liang MongKoh等人基于二维机器视觉提出了两种精确丈量焊球高度的方法,一种利用构造光识别算法,另一种利用自动聚焦过程处理。两种算法的丈量准确度都可以达到±1 μm。2007年Perng D.B.等人利用LED搭建了用于键合线检测的可调空间构造光系统。该系统供应可控的不同方向的光源,与成像系统合营可以实现二维或三维的芯片整体键合线检测。
在办理空间繁芜走线问题方面,1997年S.H. Ong等人提出利用单摄像头多角度成像实现键合线的3维建模,并建立了干系的算法。2000年Q.Z. Ye等人单摄像头旋转芯片的方法,实现了键合线的3维建模,并通过模型剖析和算法优化实现了运算速率的提高。2010年Der-Baau Perng等人为理解决高密度多层键合线剖析的困难,通过分别采集引线框、焊点位置和引线交错信息实现了高速自动识别多层走线间的关系。
在新方法实现分外成像方面,2011年WangX.Y.等人提出了以激光通过狭缝形成的干涉条纹作为光源,利用键合线对干涉条纹的扰动实现微键合线描述的识别。2014年Kongjing Li等人提出的涡流脉冲热成像法(eddy current pulsed thermography,ECPT)利用电磁感应事理以脉冲式的涡流作为勉励源,并利用热成像仪对被涡流加热后的键合线进行成像。仿真和实验表明,针对普通成像无法检测出的键合线部分断裂或焊点部分脱落等毛病,该方法能够进行有效快速的检测。2014年Dietachmayr F.W.等人针对大功率器件中为提高芯片长期可靠性常用冗余焊接(多根焊线用于同一电通路)中,两根或多跟焊接线中一根涌现局部断裂等毛病时无法检测的问题,基于法拉第效应提出了键合线的电磁图像法(magneto-optical imaging)。该方法也能办理其他情形下的焊接检测问题。
5 检测方法比拟总结
本文对电子器件封装中引线键合质量的检测方法进行了详细综述。从运用的角度出发,引线键合的检测有抽检和全检。各种检测方法及其特点比拟见表1。
6 未来与展望
虽然引线键合技能经由几十年的发展,不断提高和完善,但是在该技能领域依然存在巨大的发展空间和许多未办理的问题。
首先是采取铜和铝等廉价引线材料替代金等传统引线材料所产生的新问题。在铜线键合技能中,离子间化合物形成更为困难,键合层薄,因此随意马虎形成不易检测的毛病焊点;铜键合线的硬度比金更大,又常运用于大功率器件中,温度造成的疲倦应力问题更加显著;其余由于铜的硬度高,造成适用于金线键合的检测手段运用于铜线键合时征象不同,例如球剪切力法中铜焊球会整体脱落而不是像金焊球一样被部分拨出;铜键合时更大的压力造成的焊盘变形随意马虎引起局部裂痕;铜的抗堕落性和抗氧化性不如金。现有的检测手段无法很好地办理这些问题。
其次是集成电路发展为键合技能提出新的哀求。随着芯片集成度的提高,对粗引线键合 、单焊盘多焊点、微间距引线键合和空间立体走线的需求不断加剧。针对传统封装形式设计的检测手段难以知足这些新的需求。
除了常日的集成电路芯片封装之外,人们还将引线键合技能用于MEMS微传感器、微型电感和微型弹簧等非传统运用中,这些非传统运用中的键合线常日不是标准形式,也须要针对详细运用处所进行研究。