球栅阵列封装,英文全称:Ball Grid Array,简称BGA,该项技能为运用在集成电路上的一种表面黏着封装技能,此技能常用来永久固定如微处理器之类的的装置。B球栅阵列封装(BGA)焊接失落效问题每每直接关系到器件的质量。基于此,下文针对球栅阵列封装(BGA)焊接涌现开裂问题作出了剖析。
某OEM厂商在发给客户的一批产品中,在终端市场的反馈中有一定比例的产品无法开机,经查为pcba贴片后主板上球栅阵列封装(BGA)脱落所致。绝大部分PCB焊点从焊球侧IMC层断开,其断口呈脆性断裂特色,还有少部分焊点从PCB基板断开,在前期的线路板打样中已经跟客户反馈过干系的问题。
一、球栅阵列封装(BGA)非毁坏性失落效剖析
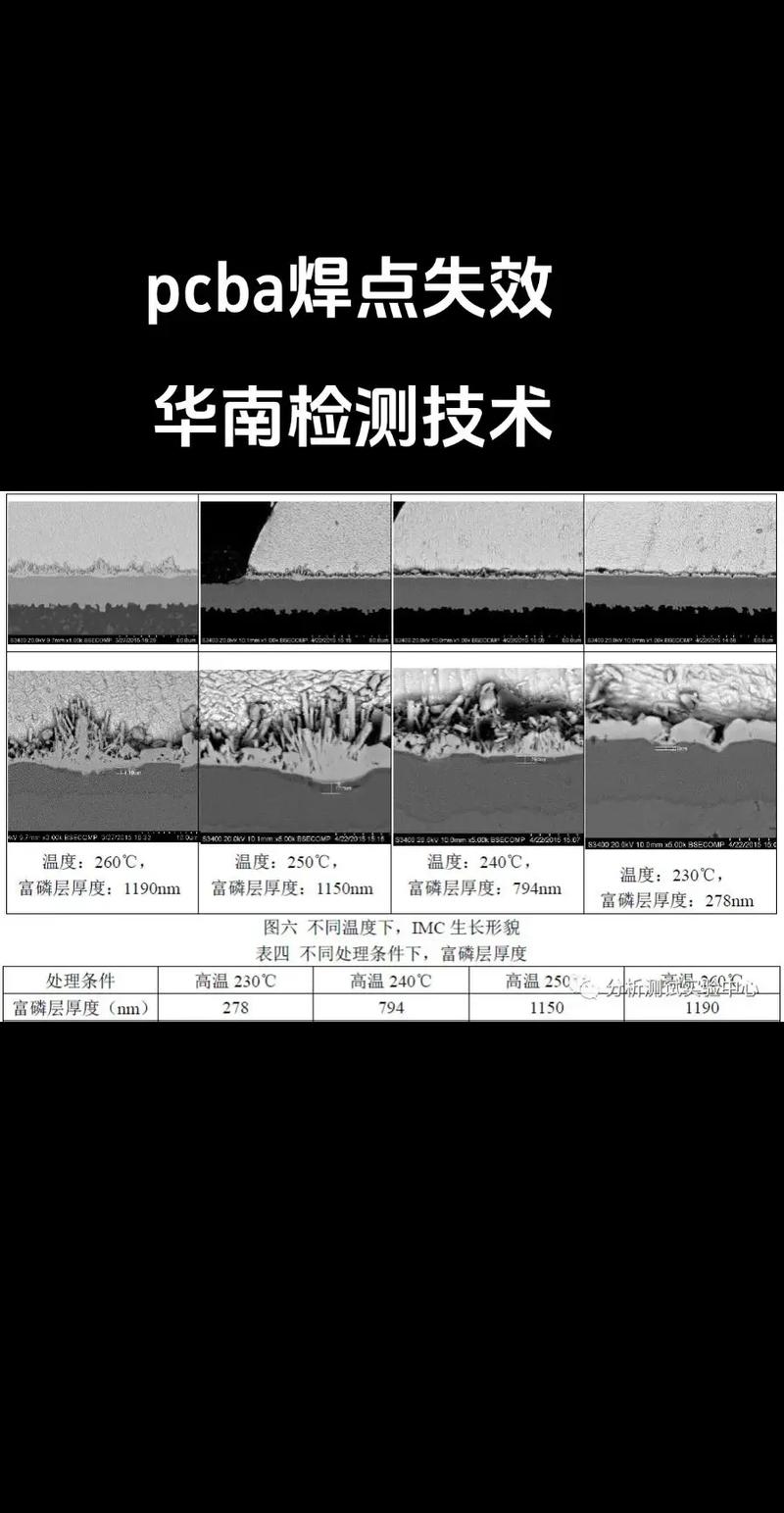
1、目视外不雅观剖析
球栅阵列封装(BGA)目视检讨常日是失落效检测剖析的第一步,便是利用人眼或借助于大略的光学放大镜和工业显微镜等,检讨球栅阵列封装(BGA)器件边缘排的焊点,探求任何可以查看到的非常,例如球窝焊点、畸形焊点和翘曲等。由于检讨常日仅限于外排焊点,有些非常可能看不到。检讨中还可以借助金属针或竹制牙签,以适宜的力量和速率划过焊点,依赖手感及目测来综合判断,特殊是虚焊或桥连的检讨,有着良好的效果。不过目视检讨存在局限性,例如重复性差、不能精确定量地反响问题,劳动强度大,一样平常不适应高品质产品和大批量集中检测。
目的:能简便、快速、直接的对焊点进行不雅观察,可以不雅观察焊点外部有没有连焊、周围表面的情形等。
但目视检测的局限性很大,只能在没有检测设备的情形下,用作初步判断,无法判断焊点内部是否存在其他毛病或焊点表面是否有空洞等。
下图为范例的机器应力导致失落效。左焊点整体开裂,右焊点无非常,且二者都呈现向内扭偏的状态。
左边焊点放大如下图:
经剖析,旁边二个焊点都呈现向内扭偏的状态,因此可推断焊点应是在成型后,受到外部应力的浸染,导致IMC整体脆断。同时应力点集中于FPC焊盘侧,表明应力可能是由FPC侧传导而来。
2、X射线检测焊点质量
实时X射线检测是一种有代价的非毁坏性检测技能,可以供应球栅阵列封装(BGA)焊点的主要信息。现在还没有哪种设备能超越实时的X射线设备。X射线检测须要干系的软件,也须要培训上岗,有履历的剖析师和无履历职员给出的检测结果差异显著。
常日球栅阵列封装(BGA)器件具有数百个引脚,其焊点可能同时具有多种焊接毛病。这时遵照合理的检测流程,既兼顾效率又不会漏掉某种毛病十分主要。球栅阵列封装(BGA)焊点质量检测合理的X射线检测流程为:
(1)先通过二维X射线检测球栅阵列封装(BGA)器件的全貌,检讨是否有焊点连接、焊球丢失和焊球位移等。
(2)然后进行器件局部检测,检讨是否有焊球位移、焊球空洞和焊球非常。二维X射线检测应采取5点检测法,着重检测器件四周及中央5点,同时,快速检测其他区域。
(3)再根据焊点是否非常的检测结果,如焊点的大小、形状和灰度,剖析是否须要进行3D断层扫描。如果球栅阵列封装(BGA)焊点形状为正常的圆形,大小和灰度都无非常,那么可不进行3D断层扫描检测;若存在焊点大小不一、形状非常、空洞较大和边界模糊等,则需对其进行3D扫描检测,进一步判断是虚焊焊点还是枕头效应等。只管3D断层扫描检测可以供应额外的焊点信息,但是这个过程可能是昂贵的。
X射线检测不雅观察到的最常见毛病之一是焊点中的空洞。根据IPC-7095C,空洞面历年夜于35%和直径大于50%是工艺掌握的极限值。一样平常来说若空洞面积总和超过焊球面积的25%即为不合格,须要返修。下图便是焊点空洞的X射线描述。虽然小的空洞可以通过检测,无需返修,但是它们仍旧是一个应把稳的工艺指标。同时还应把稳确保在图像中不存在电晕征象,由于这样可以使空洞看起来比实际的更大。
焊料桥接是可以通过X射线检讨的另一种毛病。当2个焊点由焊料连接时,焊料和周围的大部分材料之间存在着显著的密度差,以是很随意马虎识别。两焊点之间的短路结果如下图所示。
焊球丢失在X射线检测图片中的表现也极为明显。由于球栅阵列封装(BGA)焊球因此阵列办法整洁排列在器件底部,哪个相应位置短缺焊球很随意马虎被创造。下图为球栅阵列封装(BGA)焊球丢失的X射线图像。
X射线检测也很随意马虎创造焊球移位的问题,关键是须要检测焊球移位的严重程度。一样平常根据详细需求来剖断焊点是否合格,通用的判据公式为:焊球球心至焊盘圆心的间隔/焊盘直径<25%。X射线检讨也可以不雅观察到畸形焊点,只管它们的不雅观察更困难。要看到确定的毛病,常日须要极度的角度和分外处理。有些畸形焊点是无害的,如下图中不雅观察到略长的焊点。
其他畸形焊点可能便是严重的毛病,如下图不雅观察到的枕头效应。枕头效应很难通过二维X射线检测来不雅观测,须要借助3D断层扫描来检测。
虚焊也很难通过二维X射线进行检测。常常先用二维X射线对有无虚焊做初步诊断。下图为倾斜光源后焊点X射线二维图像,从图中可看到相互嵌套的3个圆。若仅能看到个中2个圆,同时焊点形状非常,如边界模糊、大小非常以及灰度较暗,那么这类焊点很可能有虚焊毛病,应进行3D断层扫描检测。
X射线检测是一种无损的物理透视方法,即为在不毁坏芯片情形下,利用X射线透视元器件,检测元器件的内部封装情形,如气泡、裂纹、绑定线非常等。常用的X射线检测办法有以下2种:
2DX-ray
对付样品无法以目视办法检测的位置,利用记录X-ray穿透不同密度物质后其光强度的变革,产生的比拟效果可形成影像即可显示出待测物的内部构造,进而可在不毁坏待测物的情形下不雅观察待测物内部有问题的区域。
目的:通过X射线扫描能快速、有效的不雅观察,能判别空焊,虚焊等球栅阵列封装(BGA)焊接毛病,球栅阵列封装(BGA)、线路板等内部位移的剖析,架桥、短路方面的缺陷等。
但2DX-ray存在一定的局限性,只能不雅观察二维平面图像,事理是将三维立体的实物样品显示在二维的显示屏上成像,对付构造繁芜的产品,不同深度方向上的信息都重叠在一起,极易稠浊。例如,在同一位置的不同面均存在元器件的情形下,焊锡形成的阴影会重叠起来,影响检测结果的准确性,因此,对付构造繁芜的产品常用作初步、快速剖断。
3DX-ray(CT扫描)
3DX-ray很好的办理了2D X-ray的局限性问题,能够呈现三维立体图像,且具有高密度分辨率和高空间分辨率,还能实现仿照断层扫描图像等。对付球栅阵列封装(BGA)焊点的毛病问题能完美的办理。
目的:可以清晰、准确的不雅观察球栅阵列封装(BGA)焊点的焊接质量和构造毛病,还能显示有缺点在焊接内部的形状、位置和大小。
在上述的非毁坏性检测方法对焊点毛病进行检测的过程中,目视检测和2DX-ray均存在局限性,而3DX-ray(CT扫描)是目前最前辈的无损检测技能能完美办理焊点毛病问题,但测试用度较昂贵,如产品可以被毁坏,则可以利用接下来要讲的毁坏性检测方法来进行测试。
二、创造问题,办理问题
剖析由于范例的机器应力导致球栅阵列封装(BGA)失落效,就须要对产线制程进行应力检测。
产线范例的应力制程有:SMT制程、分板制程、ICT、FCT、打螺丝组装等制程。
三、对球栅阵列封装(BGA)进行毁坏性失落效剖析
1、染色(红墨水)试验检测焊点质量
染色测试是通过高渗透性高着色性染料红墨水渗透到焊点开裂区域,然后拉开焊点,不雅观测焊点内部开裂程度和分布,是一种本钱效益的毁坏性检测技能,供应焊点界面的所有信息。首先采打水润滑切片锯(首选)或旋转工具取下含有所需球栅阵列封装(BGA)的PCBA部分。应留下足够的板材以便操作。将球栅阵列封装(BGA)在助焊剂去除剂中浸泡3h,去除所有残留的助焊剂,使红墨水可以渗透到任何裂纹或分离处。随后用酒精冲洗和风干,以确保所有的助焊剂去除剂被去除。然后球栅阵列封装(BGA)在一个局部真空下染色6min,用气罐吹走多余的红墨水,在100℃烤箱中至少干燥3h。样品也可以在室温下干燥,但须要至少48h,确保红墨水干燥。这一步至关主要,由于在操作过程中任何不干的红墨水都可能会导致缺点的迹象。然后利用试验台把球栅阵列封装(BGA)从基板上拉下。这时所有的焊点都被从最弱的界面勾引失落效。必须小心掌握拉断器件时的外力,以担保焊点连续沿预开裂区域断开。
红墨水试验适用于验证印刷电路板上球栅阵列封装(BGA)及IC的焊接情形。通过不雅观察、剖析PCB及IC组件的焊点染色情形,从而对焊接开裂情形进行剖断。
红墨水试验的事理是利用液体的渗透性。将焊点置于赤色染剂中,让染料渗入焊点裂纹,干燥后将焊点强行分离,通过不雅观察开裂处界面颜色状态来判断焊点是否断裂。大略来说,分为五步:切割 → 渗透 → 烘干 → 分离 → 不雅观察 。
目的:一样平常来说红墨水测试比较能够看到一整颗球栅阵列封装(BGA)底下的所有锡球的焊锡征象。是一种常用的电子组装焊接质量的剖析手段,可以稽核电子零件的焊接工艺是否存在虚焊,假焊,裂痕等瑕疵。
用立体显微镜检讨焊点的两侧界面,探求所有的染料标志。下图就给出了一个焊点范例的染料测试失落效界面图。
染色可以表明焊盘坑裂、界面断裂和球窝焊点等,球窝焊点的实例如下图所示。
2、金相检测
金相检测供应最好的球栅阵列封装(BGA)焊点界面数据,大多数非常都可以被终极确认。通过剖面得到的信息能够表明毛病问题是与工艺干系还是与材料干系,有助于确定须要在哪道工序办理纠正问题。但是,金相检测也有一定的不敷,检测过程是劳动力密集型的,一次只能对一个平面进行评价。此外,它须要相对昂贵的设备来完成。
此时,X射线和染色测试的结果常日是一个很好的参考依据,有助于确定评价哪个平面,可能存在什么样的毛病。如果剖面没有什么问题,常日选择对角线或边缘排,由于这些地方含有角部焊点,毛病大多数发生在这里。将样品在旋转砂轮上机器研磨,采取逐渐变细的砂磨纸,直到达到所需的焊点平面,然后利用抛光钻石粗抛光及氧化铝终极抛光。再用铜蚀刻工艺蚀刻样品,使焊点特色更加突出。大空洞、畸形焊点和球窝焊点常日在低倍率(5倍~150倍)显微镜下即可显现,而裂痕、微空洞、黑盘和焊盘坑裂毛病在较高倍率(150倍~1500倍)显微镜下才可显现。
扫描电镜(SEM)是金相检测的赞助检测工具,供应更高放大倍率的金属间化合物界面、裂痕和干系毛病的视图,为小的特性和毛病供应良好的分辨率。能量色散光谱(EDS)检测是连接到SEM的一个仪器,供应SEM中成像区域的元素数据。这是非常主要的,由于许多用于剖析的特色都是小斑点或薄层,如铜锡金属间化合物层(Cu6Sn5和Cu3Sn)等。
3、切片剖析焊点质量
切片剖析是进行PCB/PCBA失落效剖析的主要技能,切片剖析较之红墨水试验更为费时,切片剖析的流程:取样→洗濯→真空镶嵌→研磨→抛光→微蚀(如有必要)→剖析。切片质量的好坏将直接影响失落效部位确认的准确性,因此对检测职员的能力哀求很高。
切片剖析的目的:既能用于检讨PCBA焊点内部空洞,界面结合状况,润湿质量评价等,还能对电路板品质的好坏进行考验。
4、SEM&EDS联用
在切片剖析的根本上,想要进一步理解焊点毛病产生的缘故原由,可以采取SEM&EDS对焊点的失落效缘故原由进行剖析。
四、球栅阵列封装(BGA)应力测试的方法和步骤
根据IPC-9704标准,测试球栅阵列封装(BGA)应力剖析,需4个对角贴上应变片。
应力测试仪TSK-64-64C-12,应变片:TSK-1E-120-3A-11L50W05MS
1、电路板测试位置打磨处理:按照指定的测试点位对电路板进行拆 件、然后打磨平滑之后进行洗濯。
2、应变片粘贴:将应变片进行编号,然后用专用胶水 TSK-36 将应变 片粘贴在指定测试点位置。
3、链接应变测试仪和电脑:将编好号的应变片与应变测试仪和电脑 链接,打开电脑软件进行方案和参数设置。
4、进行测试和保存报表:打开应变测试软件,清零校准,然后进入 检测数据阶段,然后保存数据。
五、进行产线制程应力测试,剖析测试结果 ,调度制程
经证明,利用应变丈量来掌握印刷版翘曲对电子工业是非常有利的,而且其做为一种甄别有损制造工艺的方法早已被行业认可。然而,随着互连密度的增加且变得更脆,翘曲导致损伤的可能性也在增大。当下须要电路板代工厂和元器件供应商都在客户指定的应变水平下进行操作。
相信通过以上的几种焊点毛病检测方法的先容相信大家能够根据自身的须要进行最适宜的选择,检测实验室能供应上述所有的焊点检测做事,愿为您的产品质量保驾护航!
还有便是,在电路板产品生产的过程中如何对球栅阵列封装(BGA)焊接工艺进行改进呢?我们供应了以下的方法供大家参考互换。
六、球栅阵列封装(BGA)焊接工艺改进方法
1、电路板、芯片预热,去除潮气,对托盘封装的球栅阵列封装(BGA)要在焊接前以120℃烘烤4~6h。
2、清洁焊盘,将留在PCB表面的助焊剂、焊锡膏清理掉。
3、涂焊锡膏、助焊剂必须利用新鲜的辅料,涂抹均匀,焊膏必须搅拌均匀,焊膏黏度和涂抹的焊膏量必须适当,才能担保焊料熔化过程中不连焊。
4、贴片时必须使球栅阵列封装(BGA)芯片上的每一个焊锡球与PCB上每一个对应的焊点对正。
5、在回流焊过程中,要精确选择各区的加热温度和韶光,同时应把稳升温的速率。一样平常,在100℃前,最大的升温速率不超过6℃/s,100℃往后最大的升温速率不超过3℃/s,在冷却区,最大的冷却速率不超过6℃/s。由于过高的泰平承平和降温速率都可能破坏PCB和芯片,这种破坏有时是肉眼不能不雅观察到的。同时,对不同的芯片、不同的焊锡膏,应选择不同的加热温度和韶光;对免洗焊膏,其活性低于非免洗焊膏,因此,焊接温度不宜过高,焊接韶光不宜过长,以防止焊锡颗粒的氧化。
6、在进行PCB设计时,PCB上球栅阵列封装(BGA)的所有焊点的焊盘应设计成一样大,如果某些过孔必须设计到焊盘下面,也应该找得当的PCB厂家,确保所有焊盘大小同等,焊盘上焊锡一样多且高度同等。
总结一下
在进行球栅阵列封装(BGA)焊点检测剖析时,应遵照一个工艺流程,确保被测样本在转移到下一道测试工序之前,应网络所有的可用数据。非毁坏性检测技能供应的初步毛病信息,有助于勾引后续的毁坏性检测剖析。X射线能够检测连焊、焊球丢失、焊球移位和空洞等毛病。引入3D断层扫描后也能够检测险些所有的球栅阵列封装(BGA)常见焊接毛病。染色测试供应了所有焊点的信息,并有助于查明存在裂痕或分离的界面。金相检测与SEM和EDS相结合,供应了基板侧和元件侧焊点界面的详细信息,可以描述发生在球栅阵列封装(BGA)中绝大多数的焊点毛病及非常,有助于查到导致球栅阵列封装(BGA)失落败的根本缘故原由。
-----END-----
免责声明:我们尊重原创,也看重分享;笔墨、图片版权归原作者所有。转载目的在于分享更多信息,不代表本号态度,如有陵犯您的权柄请及时联系,我们将第一韶光删除,感激!